Cementirani karbid je praški metalurgijski izdelek, ki je sintran v vakuumski peči ali peči za redukcijo vodika s kobaltom, nikljem in molibdenom kot glavnim sestavnim delom volframovega karbidnega mikrona v prahu ognjevzdržne kovine z visoko trdoživo. Sintranje je zelo kritičen korak pri cementiranem karbidu. Tako imenovano sintranje je, da se ogreva praškasta kompaktna na določeno temperaturo, ga hranite za določeno obdobje in nato ohladimo, da dobite material z zahtevanimi lastnostmi. Postopek sintranja cementiranega karbida je zelo zapleten in je enostavno izdelati sintrane odpadke, če niste previdni. Danes bo Zhuzhou Chuangrui Cement Carbide Co., Ltd, z vami delil skupne sintrane odpadke in razloge.
1. odpadki s karbidnimi sintrami so prvi, ki se olupijo
To pomeni, da površina cementiranega karbida prehaja skozi razpoke na robovih, izkrivljenih lupine ali razpok, v hudih primerih pa majhne tanke kože, kot so ribje luske, razpoke in celo pranje. Olupljenje je predvsem posledica kontaktnega učinka kobalta v kompaktnem, tako da v njem razpade prosti ogljik, ki vsebuje ogljik, kar povzroči zmanjšanje lokalne trdnosti kompaktnega, kar ima za posledico luščenje.
2. Drugi najpogostejši odpadki s cementiranim karbidom so luknje
Pore nad 40 mikronov se imenujejo pore. Dejavniki, ki lahko povzročijo pretis, lahko tvorijo pore. Poleg tega, ko v sintranem telesu obstajajo nečistoče, ki jih staljena kovina ne navlaži, kot so velike pore, kot so "neprekinjeno", ali sintrano telo ima resno trdno fazo in segregacija tekoče faze lahko tvori pore.
3. Tretji najpogostejši odpadni proizvod s cementiranim karbidom je pretisni omot
Na površini ustreznih delov se pojavljajo luknje v cementiranih izdelkih iz karbidne zlitine, konveksne ukrivljene površine pa se pojavljajo. Ta pojav se imenuje mehurje. Glavni razlog za pretisni omot je, da ima sintrano telo razmeroma koncentriran plin. Običajno obstajata dve vrsti: ena je, da se zrak kopiči v sintranem telesu, med postopkom krčenja sintranja pa se zrak premakne od notranjosti na površino. Če v sintranem telesu obstajajo nečistoče določene velikosti, kot so ostanki zlitin, železni ostanki in kobaltni ostanki, se bo zrak tu koncentriral. Ko se sintrano telo pojavi v tekoči fazi in je zgoščeno, zraka ni mogoče odpustiti. Na najmanjših površinah se tvorijo pretisni omoti.
Drugo je, da obstaja kemična reakcija, ki ustvari veliko količino plina v sintranem telesu. Kadar je v sintranem telesu nekaj oksidov, se zmanjšajo, ko se zdi, da tekoča faza ustvarja plin, zaradi česar bo proizvod mehurček; Zlitine WC-CO so na splošno sestavljene iz aglomeracije oksidov v mešanici.
4. Obstaja tudi neenakomerna organizacija: Mešanje
5. In potem je deformacija
Nepravilna sprememba sintranega telesa se imenuje deformacija. Glavni razlogi za deformacijo so naslednji: porazdelitev gostote spojev ni enakomerna, ker je gostota končne zlitine enaka; Sintrano telo močno primanjkuje ogljika lokalno, ker pomanjkanje ogljika relativno zmanjšuje tekočo fazo; Nalaganje čolna je nerazumno; Podstavljiva plošča je neenakomerna.
6. črno srce
Ohlapno območje na površini zloma zlitine se imenuje črno središče. Glavni razlogi: prenizka vsebnost ogljika in neprimerno visoka vsebnost ogljika. Vsi dejavniki, ki vplivajo na vsebnost ogljika v sintranem telesu, bodo vplivali na nastanek črnih src.
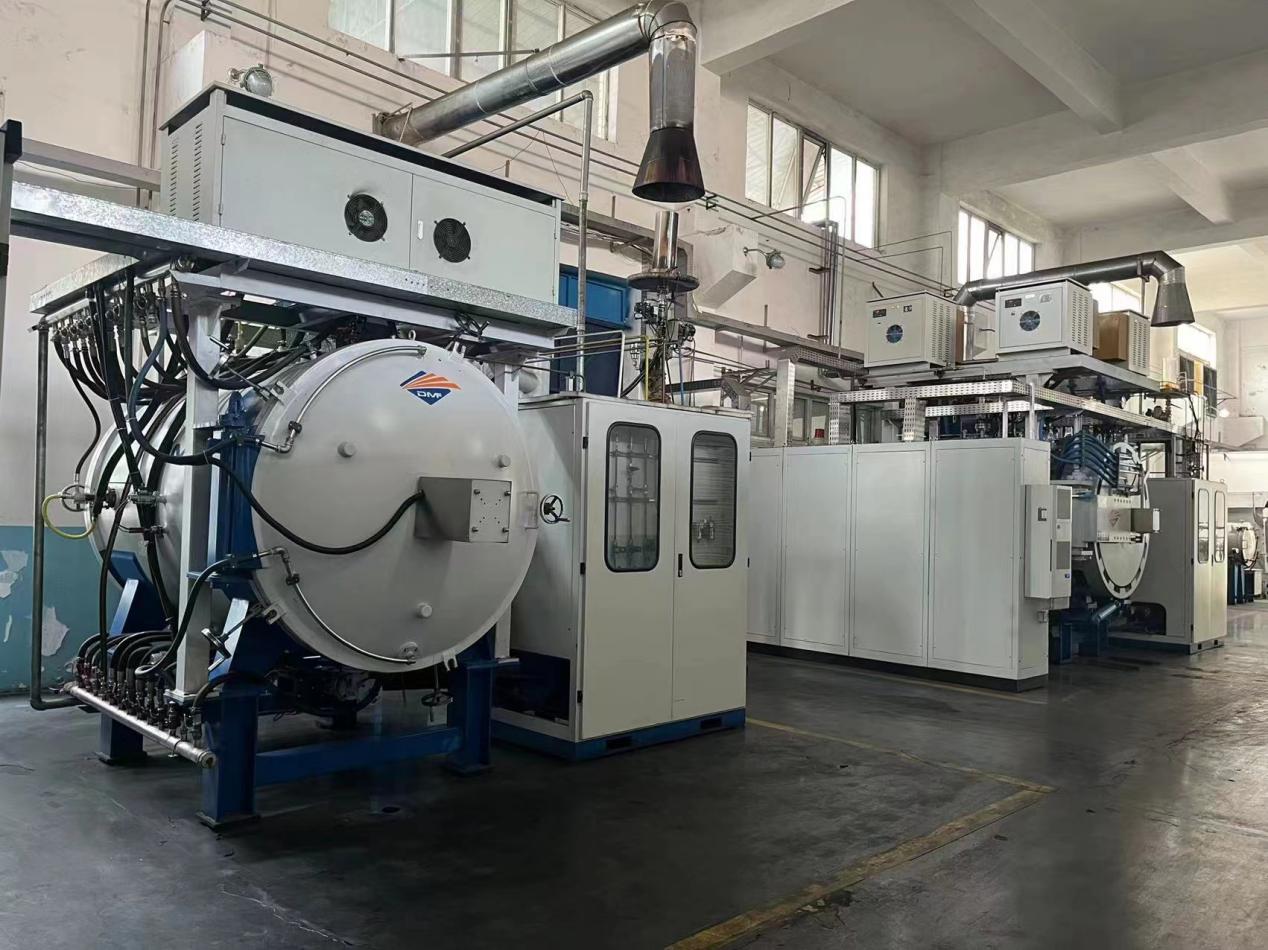
7. razpoke so tudi pogost pojav v cementiranih odpadnih proizvodih, sintranih karbidu
Stisne razpoke: Ker se sprostitev tlaka ne pokaže takoj, ko se briketa posuši, je elastično okrevanje med sintranjem hitrejše. Oksidacijske razpoke: Ker je briketa delno oksidiran, ko je suh, se toplotna ekspanzija oksidiranega dela razlikuje od neobremenjenega dela.
8. Overbing
Ko je temperatura sintranja previsoka ali je čas zadrževanja predolg, bo izdelek pretirano gorel. Prekomerna gorenja izdelka naredi zrna debelejša, pore se povečajo, lastnosti zlitine pa se znatno zmanjšajo. Kovinski sijaj izdelkov, ki so pod perjem, ni očiten in ga je treba le ponovno nabiti.
Čas objave: januar-25-2024